during the day. For example, to stay on schedule during
monthly, quarterly, or yearly processing, production
work will have to be run during the day shift. You may
also have to have additional saves run in association
with monthly, quarterly, or yearly processing. Another
example is as you are preparing to load a software
update, you might have special saves run during another
shift. This will ensure that the data is backed up and a
good copy of the software is available if the update does
not work properly. You may also have to reschedule
some of the production work.
Anytime the normal work schedule is changed, it
may affect the online users by slowing the system
response time or causing the system to be unavailable
to the users. Care must be taken when the schedule is
to be changed. Try to cause the minimum interruption
to online users, and do keep them notified of the
changes.
PRODUCTION PROCESSING
During production processing, the I/O control
clerk, production control coordinator, and operators
will monitor the schedule and the jobs to see that the
work is being accomplished as planned. When
problems arise, as they will, you may need to become
involved. You may be involved in determining the
cause of the problem and in working with the user to
solve the problem. The common causes of problems are
application program processing errors and system
downtime.
Users must be informed concerning any production
problems pertaining to their jobs. When you talk to the
users, you must know which job had the problem, what
the problem was, and what, if anything, AIS can door
did do to correct the problem. Besides notifying the
user of production problems, you will be required to
notify them of system downtime or nonavailability.
Setting up procedures for the operator and the
production controller to follow will help in solving
problems and in communications with users.
For online users, the subsystem coordinators are the
most qualified and highly trained individuals on their
particular subsystem and should be assisting users with
processing problems. This does not eliminate the need
for the operators to become knowledgeable in the
workings of each subsystem, since they normally are
called first when a problem occurs. You will need to
examine any production problems that occur and work
with the shift supervisor and/or production control
coordinator to be sure proper corrective action was
taken.
APPLICATION PROGRAM PROCESSING
ERRORS
To determine the causes of application program
errors, you have two areas of concernhardware and
software. Lets look at some of the most common
causes in each of these areas.
Hardware Problems
With respect to the hardware, not only each specific
piece of equipment is a possible cause of a problem, but
you also have external environmental concerns.
Some of the most frequent hardware problems are:
. Head crash;
. Tape drive damage to a tape; and
. Tape read/write errors.
If tape read/write errors cannot be conected by
cleaning the read/write heads, a maintenance technician
should be called. For head crashes and tape drive
damage, a maintenance technician should always be
called.
The most common external environmental
problems are:
l Loss of power;
l Voltage spikes; and
l Loss of air conditioning.
What action should be taken will depend on the
damage done. The operator may be able to recover the
job completely by rebooting and restarting the job. If
the data files have been corrupted, the operator may
need assistance from the user and/or the media librarian.
Software Problems
Examples of the common software problems are:
l Wrong file specified;
l Program entered a loop; and
l File not available.
The preceding is only a very brief list of possible
problems. There are too many different causes to list in
1-19
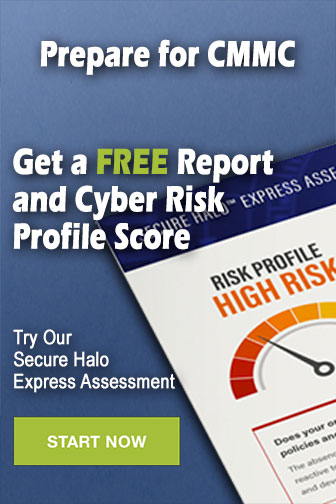